McKinney Concrete is one of the most popular construction materials used today. It is found in a number of structures from tunnels to high-rise buildings and is extremely durable.
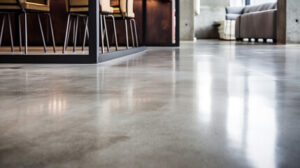
Concrete consists of aggregates like sand and gravel, and binding material like cement. It is mixed with water and undergoes a reaction called hydration that hardens the concrete.
Concrete is one of the most popular construction materials around because it is very strong and can stand up to high loads. In addition, it is a durable material that can be used for a wide variety of projects, from residential homes to commercial parking lots. It also holds up well against harsh weather conditions, environmental wear and tear, and heavy traffic, making it ideal for areas that need to withstand heavy use.
To create this remarkable construction material, water, aggregates (crushed stone, gravel or small pea gravel), and cement are mixed together to form a dense, sturdy substance. The strength of a concrete mix is dependent on the ratio of these ingredients, but many manufacturers also incorporate silica fume or pozzolic admixtures into their mix to increase its overall strength. In some cases, concrete may also contain steel reinforcing bars to increase its tensile strength and enhance its durability.
When a mixture of concrete is poured on-site, it is often vibrated to ensure that the aggregates are tightly packed together to avoid air pockets and voids. The vibrating process also improves the bond between the concrete and the steel reinforcing bars. This is an important step because it allows the concrete to better withstand tension and compressive forces, which makes it an excellent choice for load-bearing structures like roads, bridges, and skyscrapers.
Concrete is available in a variety of different strengths to meet the unique needs of each project. For example, some concrete mixes are designed with a high early strength so that it can achieve its full strength within 24 hours after being poured. This means that the formwork can be removed earlier and the building construction is able to progress more quickly.
Durability
Concrete is a durable material that can last longer than most other building materials. It can withstand environmental factors and chemical attacks. This makes it a popular choice for construction, especially when combined with steel reinforcing bars and fibers that improve tensile strength. However, if proper maintenance and repair practices aren’t employed, concrete structures can deteriorate faster than they should.
The durability of concrete depends on several factors, including the mix design, curing process, and environmental conditions. Insufficient consideration of these factors can lead to premature deterioration, costing the industry billions of dollars annually. Improving the durability of concrete could help reduce these costs, as it would allow structures to maintain their intended performance over a longer period of time, reducing annualised embodied environmental impacts.
Many different factors impact the durability of concrete, from contaminated aggregates that cause pop-outs or alkali silica reactivity to off-spec cement that leads to finishing issues and inconsistent setting times. Additionally, frequent wetting and drying can result in crazing, scaling, and loss of strength. To avoid this, the concrete must be protected against freeze-thaw damage, which can be achieved through a pre-mixed deicer spray like Aquapel, that prevents the migration of up to 90 percent of the chloride ions from salt used as deicing agents.
To maximize the durability of concrete, it is critical to adhere to strict construction standards and to use high-quality, consistent raw materials. In addition, using concrete admixtures and reinforcement that can enhance specific engineering properties will improve the long-term performance of the structure. To ensure that concrete meets the desired performance criteria, it must be tested and monitored throughout its life cycle. Tests like the Rapid Chloride Permeability (RCP) test can determine how much resistance it has to corrosive attack, while the absorption of water can be determined by testing at different ages.
Moisture Resistance
Concrete is a resilient material, able to hold up to many different elements. However, if the concrete is exposed to too much moisture, it can become damaged and weaken. This can lead to problems with the flooring or structural integrity of the building. For this reason, commercial concrete contractors work to keep a balance of humidity and water content in the concrete during curing. Moisture can seep into concrete slabs through groundwater or rain, or even through high indoor humidity levels. Identifying where the moisture is coming from will dictate an appropriate course of action.
Traditional concrete is a porous material, with tiny holes that can draw in moisture through capillary action. Typically, this is a good thing. It helps concrete block walls resist the formation of efflorescence, a chalky powder that can look furry or crystal-like and is commonly found in older, unfinished block buildings.
However, excessive or uncontrolled moisture can damage concrete in a variety of ways, including corrosion and deterioration of the aggregate and cement, and spalling of the surface. The use of admixtures and low water-to-cement ratios help to protect concrete against these types of moisture damage.
Moisture can also cause damage by evaporating into the air, causing mold and mildew to form in concrete floors. To prevent this, moisture meters can be used to measure the level of vapor escaping the concrete.
Certain additives can be mixed into concrete to improve its water resistance, as well as adding waterproof sealants and coatings. These products are designed to prevent moisture from penetrating concrete and can also provide additional strength and durability. These products can be particularly useful in areas with a lot of salt or sulfates, which can cause damaging chemical reactions with concrete.
Heat Resistance
Concrete is a mix of aggregates and binding materials. It has great compressive strength, allowing it to withstand significant squeezing pressure from gravity or heavy direct loads. However, it has very little tensile strength and will fail if it is subjected to any sort of bending or twisting force. To prevent this from happening, concrete is often reinforced with some type of tensile material, usually steel mesh. This can be a network of individual steel reinforcing bars (known as rebar) or a heavier version of this known as welded-wire fabric.
Heat resistant concrete is a special form of concrete that is designed to withstand extreme heat environments. It has an excellent thermal capacity and is an effective insulator, which helps reduce energy consumption and minimizes heat transfer. This makes it ideal for use in industrial, commercial, and residential applications.
This kind of concrete is made up of aggregates and a binding material that has been treated to improve its ability to resist heat. Typically, this involves increasing its thermal conductivity, minimizing its expansion rate, and improving its resistance to corrosion. While there are a number of different types of concrete that can be used for this purpose, it is important to choose the right mixture for your specific application.
To improve the tensile and flexural strength of heat resistant concrete, researchers have tested several additives, including silica fume, fly ash, ground pumice, and metakaolin. While many of these additives have been shown to increase the durability of HSC, the use of these additives has also led to lower tensile and flexural strengths than those of conventional reference HSC. However, the addition of AEA seems to be a good way to improve tensile and flexural strength by reducing built-up stresses in the concrete.
Customization
Concrete is an important construction material that can be customized in a number of ways. It can be colored, stamped, and even polished to create unique architectural designs. It can also be reinforced with steel or other materials to enhance its strength. Customizing concrete allows architects and engineers to create structures that are both functional and attractive.
Concrete can be made into a wide range of shapes and sizes, and it is the most widely used construction material in the world. It is used for building homes, hospitals, skyscrapers, and even bridges. It is also the linchpin of our transportation infrastructure, from roads and highways to railway stations and airports.
It is a mixture of sand, gravel, stone and/or aggregates bound together by a water-based binder called cement. It can be modified by adding various additives and admixtures to change the properties of the fresh concrete mix. These changes are referred to as concrete formulation or mix design. The process of selecting the right concrete mix for a particular application is known as concrete design or design specification.
There are different kinds of concrete, depending on the type of binder used. Some common types of concrete are Portland cement, self-compacting concrete (SCC), and lightweight aggregate concrete. Some types of concrete can also be reinforced with polymer, which is called lightweight reinforced concrete or LRMC.
Concrete can be personalized to suit the needs of homeowners or commercial property owners. For instance, stained and stamped concrete can be used to create patterns that resemble natural stones or granites. This method is inexpensive and provides a high-quality aesthetic finish. A sealant can be applied to the finished concrete to protect it from damage and make cleaning easier.